ПОКРЫТИЯ ДЛЯ УЛУЧШЕНИЯ ХАРАКТЕРИСТИК ПОДШИПНИКОВ
Покрытия позволяют увеличить срок службы и оптимизировать характеристики подшипников качения и скольжения. Выбор покрытия может зависеть от рабочих условий и эксплуатационных требований. Компания SKF предлагает более 35 различных специализированных покрытий.
Считается, что подшипники качения могут работать практически бесконечно, если соблюдаются следующие условия эксплуатации:
• приложенное давление не превышает определённого значения;
• используется надлежащее смазочное вещество;
• отсутствуют загрязнения. Разумеется, в некоторых случаях условия эксплуатации значительно отличаются от идеальных или возникают непредвиденные проблемы, которые увеличивают затраты на эксплуатацию и техническое обслуживание.
Чтобы продлить срок службы подшипников и оптимизировать их характеристики в неидеальных рабочих условиях, были разработаны различные стратегии. Одной из стратегий является использование покрытия, которое может влиять на следующие характеристики:
• износостойкость;
• повышенное или сниженное трение;
• коррозионная стойкость;
• скользящие свойства;
• улучшенное смазывание или снижение потребности в смазке во время работы;
• электроизоляция;
• водородный барьер;
• защита от фреттинг-коррозии;
• улучшение внешнего вида.
Покрытие — это стандартная стальная основа подшипника, на которую нанесён материал, обладающий определёнными свойствами, значительно улучшающими рабочие характеристики. Подшипники с покрытием также могут использоваться для устранения разрыва между стандартными стальными подшипниками и гибридными керамическими подшипниками. В некоторых отраслях применяются керамические роликовые подшипники (хорошее, но дорогое решение), которые сложно найти на рынке. В таких случаях обеспечить нормальный уровень работы стандартных подшипников можно с помощью покрытия.
Некоторые покрытия наносятся очень тонким слоем, что обеспечивает важное преимущество. Покрытия толщиной всего несколько микрон позволяют использовать стандартные, серийно производимые подшипники без дополнительных затрат на перенастройку станков.
ОБЗОР ТЕХНОЛОГИЙ НАНЕСЕНИЯ ПОКРЫТИЙ
Как показано на рис. 1, в компании SKF используются различные технологии нанесения покрытий. Их можно разделить на три основные категории:
• Методы с использованием газообразного состояния, когда материал покрытия перед осаждением на поверхность преобразуется в газовую или паровую фазу. К ним относятся такие технологии вакуумного напыления, как физическое осаждение из паровой фазы (PVD) и плазмохимическое осаждение из газовой фазы (PACVD).
• Методы с использованием жидкого состояния, когда материал покрытия находится в жидкой фазе перед тем, как осесть на поверхности в виде твердых частиц. Эти методы можно разделить на категории химического (химическое осаждение, электролитическая обработка, гомогенные химические реакции, погружение и распыление жидкости) и электрохимического осаждения, например гальваническое осаждение металлического покрытия на электроде с помощью электролиза.
• Методы с использованием расплавленного материала, когда перед осаждением материал покрытия расплавляется или частично расплавляется (размягчается), а затем с помощью источника высокой мощности осаждается на поверхность в виде твердого вещества. Эти методы подразделяются на осаждение распылением (включает широкий спектр технологий с быстрым нагревом материала в горячей газообразной среде и одновременным направлением материала с высокой скоростью на поверхность для формирования покрытия) и технологию лазерной наплавки.
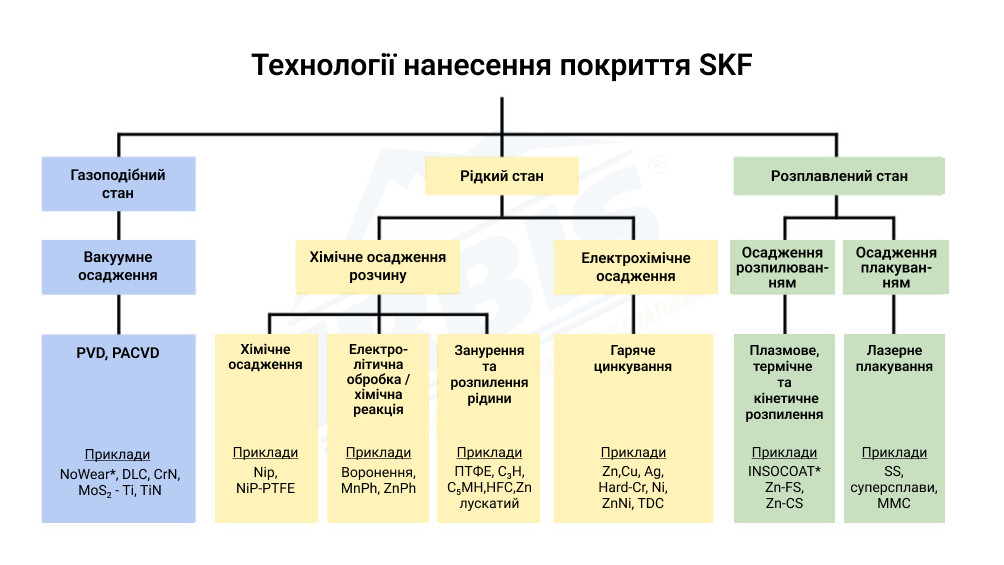
Рис. 1. Обзор технологий нанесения покрытий, используемых SKF, и примеры.
МИР ПОКРЫТИЙ SKF
Ассортимент SKF включает более 35 современных покрытий, которые можно использовать в различных областях и для разных частей подшипников. Все покрытия оптимизированы с учётом особых требований, предъявляемых к подшипникам, и выполняются в соответствии с точными спецификациями и под строгим контролем качества. Покрытия производятся на специализированных предприятиях по нанесению покрытий, требования на которых часто превышают стандарты, установленные для покрытий и оборудования, что обеспечивает максимальное качество, надёжность и воспроизводимость.
«Некоторые покрытия наносятся очень тонким слоем, что обеспечивает важное преимущество»
В этой статье рассматриваются некоторые из наиболее распространённых покрытий SKF. Полный перечень покрытий SKF вместе с их физическими, химическими и трибологическими свойствами опубликован онлайн в каталоге покрытий SKF.
ПОДШИПНИКИ КАЧЕНИЯ
На рис. 2 перечислены 12 основных покрытий, которые обеспечивают пять ключевых характеристик для подшипников качения, включая защиту сепараторов от износа при трении скольжения, электрическую изоляцию, защиту от фреттинг-коррозии, защиту от коррозии и износа дорожек качения.
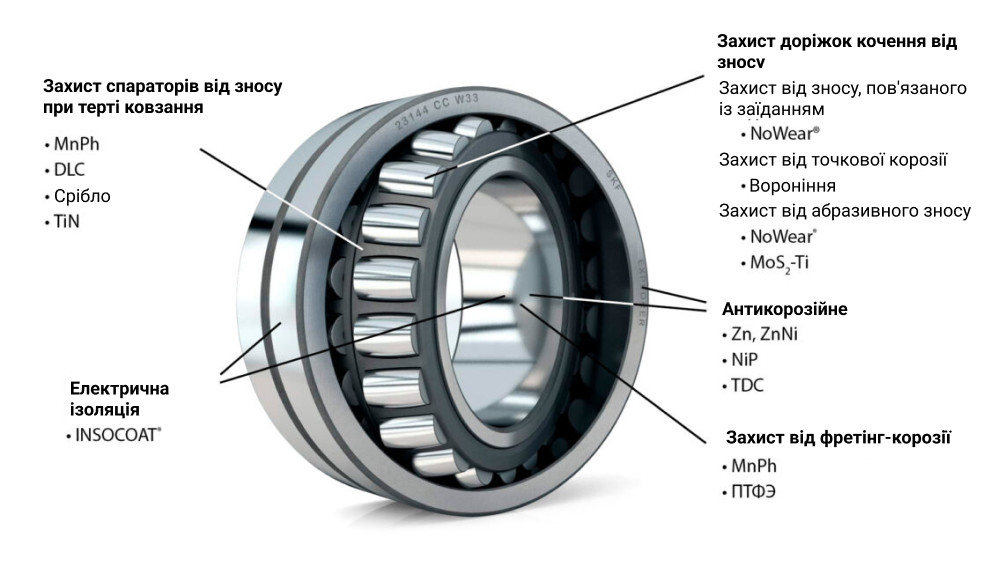
Рис. 2. Различные типы покрытий компонентов подшипников качения.
a. Защита дорожек качения от износа
Black Oxide: Обработка поверхности с помощью химической реакции на поверхности стальных компонентов подшипника. Покрытие наносится на поверхности всех компонентов подшипника. Детали погружаются в различные водно-солевые щелочные растворы при температуре 140–150 °C. В результате реакции между железом в легированной стали и реагентами формируется черный слой толщиной около 1 мкм, состоящий из хорошо сформированной смеси FeO, Fe2O3 и Fe3O4. Покрытие имеет множество преимуществ, включая минимизацию износа при трении скольжения и адгезионного износа. Оно также улучшает процесс приработки, обеспечивая очень гладкую поверхность, что приводит к более низкому стационарному трению по сравнению с подшипниками без покрытия. Другое преимущество — улучшение адгезии масла, что создает защиту от легкой коррозии. Воронение образует защитный барьер от водородной хрупкости, защищая расположенную под покрытием сталь. Кроме того, слой покрытия повышает стойкость к точечной коррозии, задиру, сколам, фреттингу, трещинам на поверхности и преждевременной усталости. Наконец, покрытие защищает поверхность от вредного воздействия противозадирных присадок (EP), которые часто применяются в маслах для редукторов ветряных турбин.
NoWear®: Компания SKF стала первым в мире производителем подшипников с углеродным покрытием. Покрытие может наноситься на поверхность всех компонентов подшипника, но наилучшие результаты достигаются при нанесении покрытия только на ролики. Детали вместе с химическими веществами размещают в вакуумной камере и используют метод PACVD. В процессе физических реакций смесь паров углерода и металла, создаваемая плазмой, конденсируется на компоненте при температуре ниже 180 °C. Получаемое темно-серое аморфное покрытие толщиной около 3 мкм характеризуется средней твердостью и очень низким трением даже в сухом состоянии. Это покрытие подходит для дорожек качения подшипников при высоком контактном давлении. Покрытие NoWear®, запатентованное в 1999 году, снижает адгезию, задиры, усталость поверхности, микроточечную коррозию и обеспечивает крайне низкий износ в условиях нехватки смазки. Кроме того, разработанное многослойное покрытие содержит специальный подслой для повышения адгезии и поверхностный графитовый слой для улучшения процесса приработки.
MoS2+Ti: Аморфный слой из дисульфида молибдена (MoS2), легированный титаном (Ti), толщиной около 1–3 мкм, который по твердости аналогичен покрытию NoWear®. Специально разработанное покрытие отличается очень низким трением и высокой износостойкостью при использовании в сухих, вакуумных средах и в условиях чистых помещений. Детали размещаются в вакуумной камере и используется метод PVD. В результате физических реакций пар, создаваемый плазмой, конденсируется на детали при температуре ниже 180 °C.
b. Защита от коррозии
Zn и ZnNi: Слои из цинка и никель-цинкового сплава толщиной 1–15 мкм осаждаются электролитическими методами и далее пассивируются для обеспечения улучшенной защиты. Обычно такое покрытие не применяется для дорожек качения подшипников. Традиционный способ защиты от коррозии — использование цинка, однако применение никель-цинкового сплава позволяет устранить некоторые недостатки исключительно цинкового покрытия, например его низкую твердость. Помимо антикоррозийных свойств, цинк обеспечивает высокий коэффициент трения, что можно использовать для противоскольжения и защиты от фреттинг-коррозии наружных поверхностей подшипника, внутренних отверстий или отверстий в корпусе подшипников.
NiP: Слой из никель-фосфорного сплава серебристого цвета толщиной 10–50 мкм осаждается автокаталитическим химическим методом. Используются три варианта с разной концентрацией фосфора в диапазоне 6–14%. Увеличение концентрации фосфора улучшает антикоррозионные свойства, но снижает твердость и износостойкость. Такие покрытия обычно применяются там, где требуется комбинация антикоррозионных и противоизносных свойств, за исключением дорожек качения. При этом покрытия толщиной менее 3 мкм также могут использоваться для дорожек качения.
TDC (хромовое покрытие низкой плотности): Поликристаллическое хромовое покрытие серебристого цвета толщиной 2–5 мкм. Покрытие наносится методом электролиза с использованием хромового кислотного электролита. Для образования тонкого слоя хрома с узловатой структурой процесс дополнительно катализируется, например, с помощью дихромата калия. Слои TDC могут наноситься как на дорожки качения подшипников, так и на наружные поверхности.
c. Защита от фреттинг-коррозии
PTFE: Полимерное покрытие толщиной 10–20 мкм. Порошок политетрафторэтилена (ПТФЭ) распыляется на поверхность методом воздушного или электростатического напыления, формирование слоя происходит в процессе термического спекания. Покрытие отличается превосходными антифрикционными свойствами, очень низким коэффициентом трения и обеспечивает защиту от прерывистого скольжения. Оно придает подшипникам свойства постоянной и эффективной защиты от фреттинг-коррозии внутренних или наружных диаметров колец подшипников.
d. Электрическая изоляция
INSOCOAT®: Это электроизоляционный слой оксида алюминия толщиной 100–300 мкм, который наносится плазменным напылением в атмосферной среде. Расплавленные частицы Al₂O₃ распыляются на стальную подложку и заполняют пористую структуру. Дополнительный этап финишной шлифовки помогает обеспечить корректные размеры подшипников. Покрытие наносится либо на наружные поверхности наружного кольца подшипника, либо на внутреннюю поверхность канала внутреннего кольца. Основные преимущества покрытия INSOCOAT® связаны с электрической изоляцией, которая препятствует прохождению электрического тока через подшипник, вызывающего эрозию поверхностей качения.
e. Защита сепараторов от износа при трении скольжения
Ag: Слои серебра (Ag) толщиной 2–4 мкм осаждаются гальваническим способом. Для увеличения адгезии серебра обычно используется медная подложка. Это мягкий металлический слой с характеристиками сухой смазки, применяемый при высоких температурах и в вакуумных средах. Данное покрытие обладает выдающейся электропроводностью и обеспечивает хорошую антикоррозионную защиту от воздействия химических веществ (умеренные щелочи и кислоты). В основном такое покрытие наносится на стальные сепараторы и в редких случаях на кольца и ролики для областей применения с высокими требованиями, например, в качестве сухой смазки в вакуумных средах, в пищевой и аэрокосмической промышленности.
TiN: Покрытие из нитрида титана (TiN) представляет собой слои золотистого цвета толщиной 1–5 мкм. Детали размещаются в вакуумной камере и используется метод PVD. В результате физических реакций пара, образующаяся азотной плазмой, распыляется с титаново́й мишени и конденсируется на детали при температуре ниже 180 °C. Такие покрытия используются для защиты от износа сепараторов в условиях наличия смазок, а также для внутренних втулок подшипников в пищевой промышленности.
ПОДШИПНИКИ СКОЛЬЖЕНИЯ
На рис. 3 представлены восемь основных покрытий, которые придают подшипникам скольжения три ключевых свойства: антикоррозийные и износостойкие покрытия для подшипников с густой смазкой или без неё.
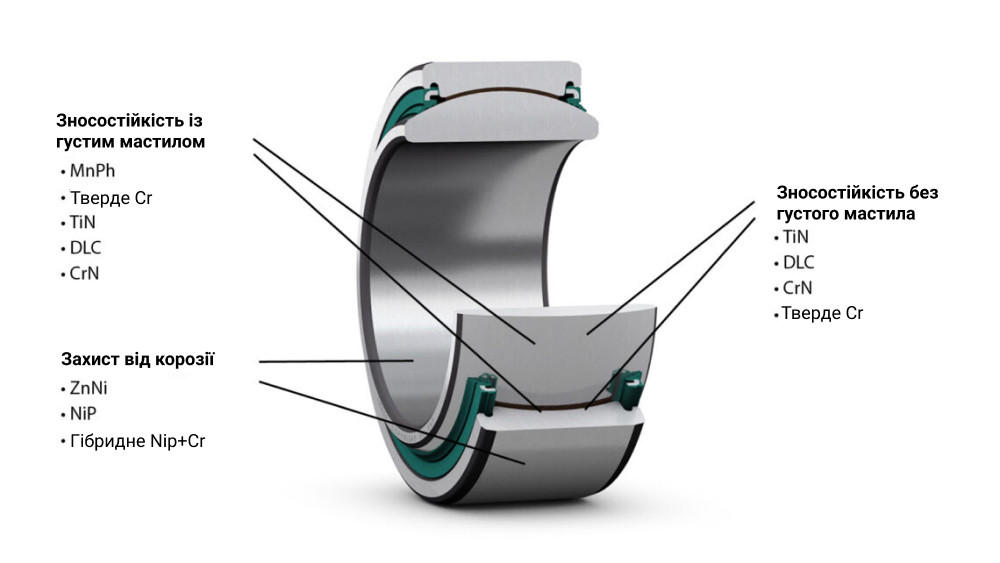
Рис. 3. Различные типы покрытий для компонентов подшипников скольжения.
a. Защита дорожек качения от износа
Твердое хромирование
Это покрытие представляет собой твёрдый слой хрома (Cr) серебристого цвета толщиной 3–15 мкм, осаждённый методом электролитического осаждения с использованием кислотного электролита с хромом. Процесс завершается очисткой, удалением шестивалентного хрома [Cr(VI)] и нанесением защитного масла. Покрытие обеспечивает хороший контакт скольжения между компонентами подшипника скольжения, отличается высокой твёрдостью и высокой износостойкостью. Нанесённый слой хрома содержит микротрещины, что ограничивает антикоррозионные свойства при небольшой толщине покрытия.
CrN: Покрытие из нитрида хрома (CrN) представляет собой нанесённый методом PVD слой серебристо-серого цвета толщиной 1–6 мкм. Детали размещаются в вакуумной камере, где твёрдотельные мишени из чистого хрома бомбардируются ионами плазмы Ar+N, которые испаряют хром (металлизация напылением). Атомы Cr соединяются с N и конденсируются на деталях при температуре ниже 180 °C. В результате образуется твёрдое покрытие, которое хорошо защищает от износа при трении скольжения, а также обеспечивает защиту в некоторых коррозионных средах. Покрытие также может применяться в подшипниках качения совместно с кольцами с покрытием CrN и роликами с покрытием NoWear®. Кроме того, покрытие используется как подложка для других покрытий с целью увеличения стойкости к контактному давлению.
DLC (алмазоподобный углерод): Это общее название группы углеродных покрытий, содержащих смесь графитовых и алмазных микроструктур. Такие покрытия могут содержать или не содержать водород, толщина покрытий обычно составляет 2–4 мкм. Обрабатываемые детали помещаются в вакуумную камеру, где на поверхность компонентов подшипников наносится несколько слоёв методом PVD или PACVD в зависимости от области применения. Состав слоёв влияет на свойства покрытий. Покрытия DLC предназначены для эксплуатации в условиях высокого износа и недостатка смазки. Такие покрытия отличаются высокой стойкостью к износу при трении скольжения и адгезионному износу, способностью выдерживать высокую нагрузку, отличной абразивной защитой и низким трением, а также обеспечивают защиту поверхности при недостатке смазки. Покрытия DLC идеально подходят для подшипников скольжения, линейных приводов, подшипников валов, втулок, штифтов, взаимодействующих с кулачками, и скользящих деталей в подшипниках качения (например, сепараторы и уплотнения). Разработанное металлокерамическое покрытие NoWear® также относится к этому семейству углеродных покрытий; однако имеются некоторые отличия. Показатели твёрдости покрытий DLC для подшипников скольжения находятся в диапазоне 18–30 ГПа (1800–3000 HV по Виккерсу), а покрытий NoWear® (используются в подшипниках качения) — около 12 ГПа (~ 1200 HV).
b. Износостойкость с густой смазкой
MnPh: Марганцево-фосфатное покрытие (MnPh) — серый или чёрный слой толщиной 2–15 мкм. Покрытие наносится путём химической реакции, обычно на поверхность всех деталей. Детали погружаются в раствор фосфатирования, содержащий марганец, при этом железо в деталях реагирует с катионами марганца и анионами фосфата в растворе. Покрытие обладает свойствами защиты от износа и фреттинг-коррозии, что значительно улучшает защиту от заедания и повышает стойкость к микроточечной коррозии. Покрытие также обеспечивает защиту при низкой относительной диэлектрической постоянной (каппа) и характеризуется улучшенной адгезией к маслу. Кроме того, покрытие MnPh отличается хорошей защитой от коррозии (в смазанном состоянии) и электроизоляционными характеристиками.
c. Защита от коррозии
Гибридное покрытие NiP+Cr: Это твёрдое покрытие, состоящее из никель-фосфорного и хромового слоёв общей толщиной 10–30 мкм. Процесс нанесения покрытия состоит из двух отдельных этапов. Сначала на поверхность для улучшения защиты от коррозии и обеспечения химической стойкости наносится слой NiP химическим способом, затем методом электролитического осаждения добавляется твёрдый слой хрома, который обеспечивает механическую прочность.
Путь к устойчивому развитию
Устойчивое развитие в сфере подшипников включает такие аспекты, как сохранение энергии и ресурсов, минимизация отходов, повышение эффективности процессов и использование возобновляемых материалов. Компания SKF — мировой технологический лидер, который рассматривает технические преобразования как ответственность и отличную возможность. Повторное использование промышленных материалов и компонентов, например масел и подшипников, может стать отличным началом. Предложения, от простых уплотнений и подшипников до ключевых промышленных компонентов и систем, помогают, например, разрабатывать лёгкие решения с низким трением для автомобильной промышленности, что способствует сокращению выбросов CO2. Другой подход, соответствующий целям устойчивого развития, — использование технологий покрытий, которые в некоторых сферах применения снижают трение (и, соответственно, энергопотребление) и увеличивают срок службы подшипников (тем самым уменьшая расход сырья).
Заключительные замечания
Использование покрытий для подшипников вызывает всё больший интерес. Выбор материалов и структуры покрытий позволяет создать изделие с уникальными физическими, механическими и трибологическими свойствами для удовлетворения постоянно растущих технологических потребностей. В частности, проводился тщательный анализ покрытий SKF с целью достижения оптимальных характеристик; в некоторых случаях, в зависимости от различных областей применения, процессы были скорректированы с превышением требований стандартов DIN и ISO.
В этой статье кратко описаны некоторые типы покрытий SKF и поясняются некоторые терминологические и технические аспекты, а также конструкция покрытий.